How Calcium Carbonate Enhances Plastic Manufacturing?
Calcium carbonate is widely used in the plastic industry as an important additive and filler material. Its unique properties and versatility make it a valuable component in various plastic applications.
At Al-Tajyr, we know how important it is to deliver high-quality raw materials to support your production goals. One of the most versatile and cost-effective additives in plastic manufacturing is calcium carbonate.
Here’s how calcium carbonate in plastic industry helps improve performance, reduce costs, and boost durability in various applications.
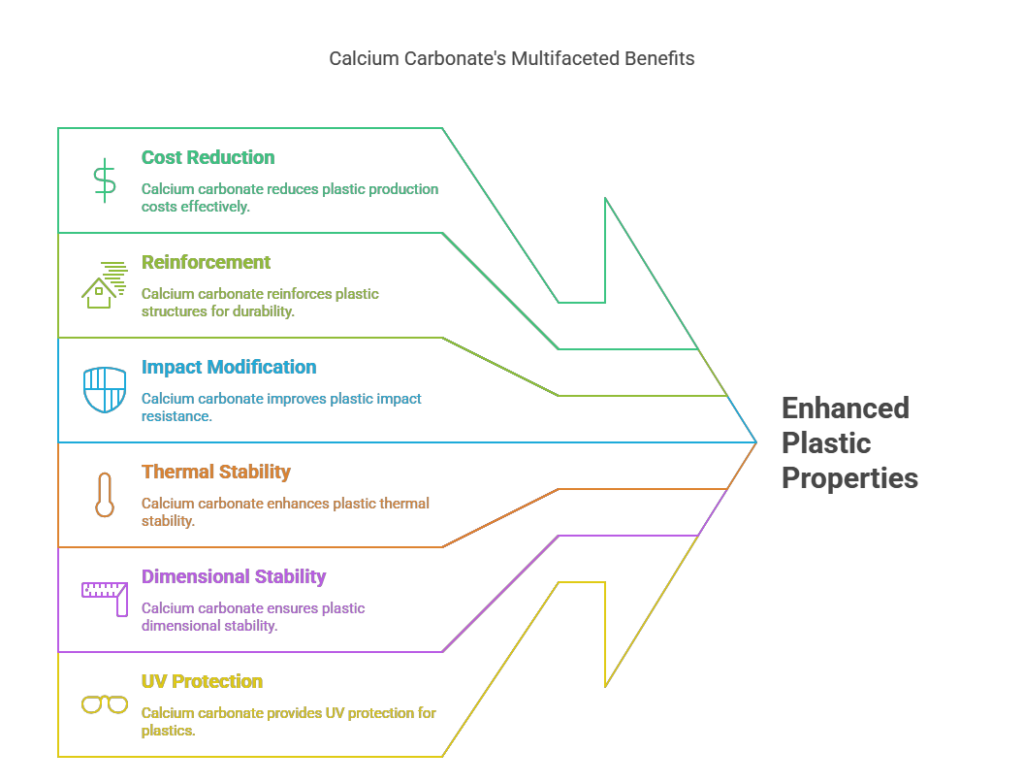
1. Cost-Effective Filler Material
Calcium carbonate is commonly added as a filler to plastic resins. Not only does it increase the volume of the material, but it also helps cut production costs. As a result, manufacturers can reduce their use of expensive resin without compromising quality or strength.
2. Mechanical Reinforcement
This compound also improves strength and stiffness. By reinforcing the plastic structure, calcium carbonate helps maintain product integrity. That’s why it’s especially valuable in demanding applications like pipes, automotive parts, and containers.
3. Better Impact Resistance
Additionally, calcium carbonate enhances impact resistance. It strengthens the plastic, helping prevent cracks or breaks under stress. For manufacturers working with blow molding or injection molding, this benefit leads to tougher and more reliable products.
4. Improved Thermal Stability
Because of its thermal stability, calcium carbonate protects plastics from heat damage. When added to formulations, it helps maintain material properties during high-temperature processes or long-term heat exposure.
5. Dimensional Accuracy
Calcium carbonate also ensures better dimensional control. It minimizes shrinkage and warping, resulting in products that keep their shape and size. This accuracy is critical for parts that require tight specifications and precision fitting.
6. Antistatic Properties
In certain products, static buildup can cause issues. Calcium carbonate can be used to reduce static electricity, especially in environments that involve electronics or dust-sensitive operations. This makes the product more functional and user-friendly.
7. UV Protection
Although not always the primary UV stabilizer, calcium carbonate helps plastics resist sunlight damage. It reduces the effects of UV exposure, extending the life of outdoor or high-exposure plastic goods.
The specific amount and type of calcium used in plastic production may vary depending on the specific requirements of the plastic and the intended application. Manufacturers carefully select the appropriate calcium carbonate grade to achieve the desired effects on the plastic’s properties.
Overall, calcium carbonate plays a vital role in the plastic industry, providing benefits such as cost reduction, reinforcement, impact modification, thermal stability, dimensional stability, antistatic properties, and UV protection.
Its versatile properties make it a valuable additive in plastic production, contributing to the overall quality, durability, and performance of various plastic products.
To order send WhatsApp