Filler Masterbatch, particularly Calcium Carbonate (CaCO3) Filler Masterbatch, has become a key ingredient for cutting production costs, boosting product strength, and improving performance.
Filler Masterbatch allows manufacturers to maintain high-quality products while reducing the need for costly virgin resin. Whether it’s for Injection Moulding, Extrusion, Blow Moulding, or Film Blowing, It is essential for enhancing efficiency and staying competitive in the market.
This enables customers not only to reduce production costs by 20% but also to enhance their competitiveness in the global market.
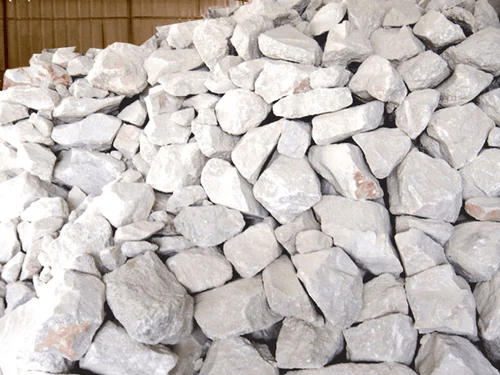
Key Industries and Applications of Filler Masterbatch:
It is used across a variety of industries, each with specific production needs and benefits. including:
- Injection Moulding.
- Blow Moulding.
- Extrusion
- Rafiaa.
- Film.
1. Filler Masterbatch in Injection Moulding:
What is Injection Moulding?
Injection molding is a process utilized for creating components from thermoplastic materials. In this method, molten plastic is injected under high pressure into a mold, which is shaped inversely to the desired product. Injection molding is a popular method for producing a diverse range of parts, from the tiniest elements to entire car body panels.
As a result, industries widely use it to create essential components for household goods, automotive parts, and industrial equipment. Furthermore, this method ensures consistent quality and precision, making it a preferred choice for mass production.
How Filler Masterbatch Enhances Injection Moulding:
- Cost Savings: Reduces production costs by partially replacing virgin resin, offering a cost-effective solution without compromising quality.
- Improved Strength: Enhance the durability, and longevity of products such as household appliances, automotive components, and electronic casings.
2. Filler Masterbatch in Extrusion:
What is Extrusion?
The process of extrusion blow molding starts with the creation of a parison or tube using a die, similar to those employed in the production of plastic pipes. Blow molding is the preferred method for producing plastic bottles, including milk jugs, shampoo containers, bleach bottles, and various other products commonly found on store shelves.
In this process, plastic pellets are loaded into the machine. These pellets are then pushed forward by a screw inside a heated barrel, where the heat and friction work together to soften the plastic. The softened plastic is then extruded downwards through a circular die
How Filler Masterbatch Enhances Extrusion:
- Cost Efficiency: Reduces production costs by partially replacing virgin resin, offering a cost-effective solution while maintaining product quality.
- Enhanced Stiffness: Increase strength of extruded plastic products, ensuring durability.
3. Filler Masterbatch in Blow Moulding
What is Blow Moulding?
Blow Moulding is a highly efficient manufacturing process used to create hollow plastic products, such as bottles, containers, and tanks. By inflating molten plastic into a mould.
How Filler Master batch Enhances Blow Moulding:
- Firstly, Cost Efficiency: Reduces production costs by partially replacing virgin resin, making it an economical choice for high-volume manufacturing.
- Additionally, Strength and Durability: Enhanced strength, durability, and resistance to wear and tear, ensuring long-lasting performance.
4. Filler Masterbatch in Film
What is Film?
Film Blowing is a widely used manufacturing process that produces thin plastic films by inflating molten plastic into a bubble, which is then flattened into layers. This technique is essential for creating packaging films, agricultural sheets, and industrial films.
How Filler Master batch Enhances Film Blowing:
- Cost Efficiency: Reduces production costs by partially replacing virgin resin, offering significant savings for high-volume film production.
- Improved Mechanical Properties: Enhance the tear resistance, strength, and durability of plastic films, making them ideal for demanding applications.
The Role of Filler Masterbatch in Raffia
First: What is Raffia? Raffia is a highly versatile and durable thermoplastic material, primarily made from polypropylene (PP). Raffia is widely used across industries to create products such as agricultural bags, packaging materials, and construction fabrics. Its ability to withstand heavy loads and harsh environmental conditions.
However, the production of raffia products can be costly due to the raw materials involved. This is where filler masterbatches come into play. By incorporating Filler Masterbatch into the Raffia production process, manufacturers can significantly reduce costs while maintaining or even enhancing the material’s strength, durability, and performance.
Second: The Role of Filler Masterbatch in Raffia
Filler masterbatches are concentrated blends of calcium carbonate (CaCO3) or other mineral fillers, polymers, and additives. They are mixed with the base polymer during manufacturing to improve the production of raffia. Here’s how they help:
- Cost Savings: Filler masterbatches reduce the need for expensive base polymers, cutting production costs significantly.
- Stronger Products: They enhance the strength and durability of raffia, making it ideal for products that face heavy use.
- Improved Processability: Filler masterbatches improve the polymer’s flow, making it easier to extrude and shape into the desired forms.
- Eco-Friendly: By reducing the use of virgin polymers, filler masterbatches support sustainability and lower the environmental impact of production.
Related Topics: Calcium Carbonate Essential Uses in Multiple Industries
For mor information contact us via whatsapp